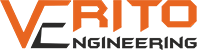
At Verito, we understand the critical role agitation plays in ensuring efficient and successful chemical reactions. As a leading manufacturer of chemical reactor agitators, we are committed to providing solutions that optimize your processes and maximize your yields within the demanding world of chemical production.
Unparalleled Expertise in Chemical Reactor Mixing:
Our team of highly qualified engineers possesses in-depth knowledge of chemical reaction processes and fluid dynamics. This expertise allows us to design and manufacture agitators that:
Custom-Designed Solutions for Every Process:
Verito understands that no two chemical reactions are alike. That's why we offer a wide range of customizable agitator solutions to cater to your specific needs. Our design considerations include:
Engineered for Performance and Reliability
Verito agitators are built to the highest standards of quality and engineering excellence. We utilize:
Diverse Applications Across the Chemical Industry
Verito agitators find application in a wide range of chemical processes, including:
Motor Power | Upto 100 kW |
Shaft Diameter | 30-300 mm |
Impeller-Systems | Verito’s high-efficiency impellers and conventional impellers |
Operating Temperature | -40℃ to 200℃ |
Operating Pressure | FV to 10 Bar |
Impeller Type | Hydrofoil, Wide Foil, Turbine |
Shaft Sealing | Single Mechanical Seal, Double Mechanical Seal with Thermosyphon Pot |
Materials (Wetted Parts) | CS, SS, Duplex & Super Duplex SS, Alloy, |
Unparalleled Quality and Reliability
Quality is at the core of everything we do at Verito. Our chemical reactor agitators undergo rigorous testing and quality control measures to ensure they meet the highest standards of performance and reliability. We use only the finest materials and components, ensuring longevity and consistent operation in demanding environments
Client-Centric Approach
We pride ourselves on building strong, lasting relationships with our clients. Verito’s client-centric approach ensures that we not only meet but exceed your expectations. From initial consultation to post-installation support, we are dedicated to your success.
Choose Verito for your chemical reactor agitator needs and experience the difference that quality, innovation, and personalized service can make. Contact us today to learn more about our products and how we can help optimize your chemical processing operations.
These mixer agitators are comes in several specifications as per the need of our customers. The offered mixer agitators are tested from our end in order to deliver a defect free range to customer's end. Our mixer agitators are developed with quality material under the direction of skilled professionals.
We ensure the highest quality & performance of our Agitators. At the same time, we have a very strong performance track record of supplying various types of agitators for various applications.