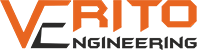
A Caustic Dosing System is a specialized equipment designed for the precise delivery and controlled addition of caustic solutions (such as sodium hydroxide or potassium hydroxide) into various industrial processes. This system is essential for applications that require accurate dosing to maintain chemical balances, ensure process efficiency, and enhance safety.
At Verito Engineering Private Limited, we specialize in providing comprehensive engineering analysis and calculations for Skid-Mounted Chemical Injection Packages, ensuring superior performance, reliability, and compliance with global industry standards.
Our expertise covers Finite Element Analysis (FEA), Computational Fluid Dynamics (CFD), Structural, Mechanical, Hydraulic, and Thermal Calculations for all critical skid components, including:
Pressure Vessel Calculations | API 675-Compliant Dosing Pump Selection & Sizing | Agitator & Mixing Calculations (For Chemical Preparation Skids) |
---|---|---|
|
|
|
Automation & Instrumentation for Optimized Operations | Piping Stress & Pressure Calculations | Structural & Skid Frame Analysis |
|
|
|
Strainer Calculations | Safety & PSV Sizing Calculations | Injection Quill |
|
|
|
Material Selection & Corrosion Analysis | Operational Efficiency & Cost Reduction | |
|
|
Key Features and Benefits
Technical Specifications
Applications
System Components
Advantages
Why Choose Verito Engineering’s Caustic Dosing System?
The Caustic Dosing System from Verito Engineering is a robust and efficient solution for precise chemical dosing applications. Its advanced features, customizable design, and reliable operation make it an essential asset for industries requiring caustic handling and dosing. Choose Verito Engineering for unparalleled quality and performance in chemical dosing systems.